Purchasing - who’d want that job, especially in a
busy workshop? On the one hand, you’ve got all
those new tooling developments, incentives & offers
to tempt you into using a new product or system. On
the other hand, production just wants the tools it
can rely on to get the backlog of work out the door
with the minimum of hassle. And don’t ignore the
bean-counters, you’ve got to make a profit - and a
bigger one than last time in most cases! Did we hear
someone say “Venn Diagram”?
As we know, the overlapping ‘sweet spot’ is relatively
small, and giving due consideration to making the
right choice is time consuming, so more often than
not we just carry on with our go-to reliable methods:
probably good for the blood pressure, at least in the
short term, but maybe not the best for margins. If
only there was something to make the choice quick
& easy... wait, what about documented proof that
the change will be a benefit, something like examples
where it’s really worked for other companies?
Well, nothing says “hard evidence” better than a few
relevant Case Studies!
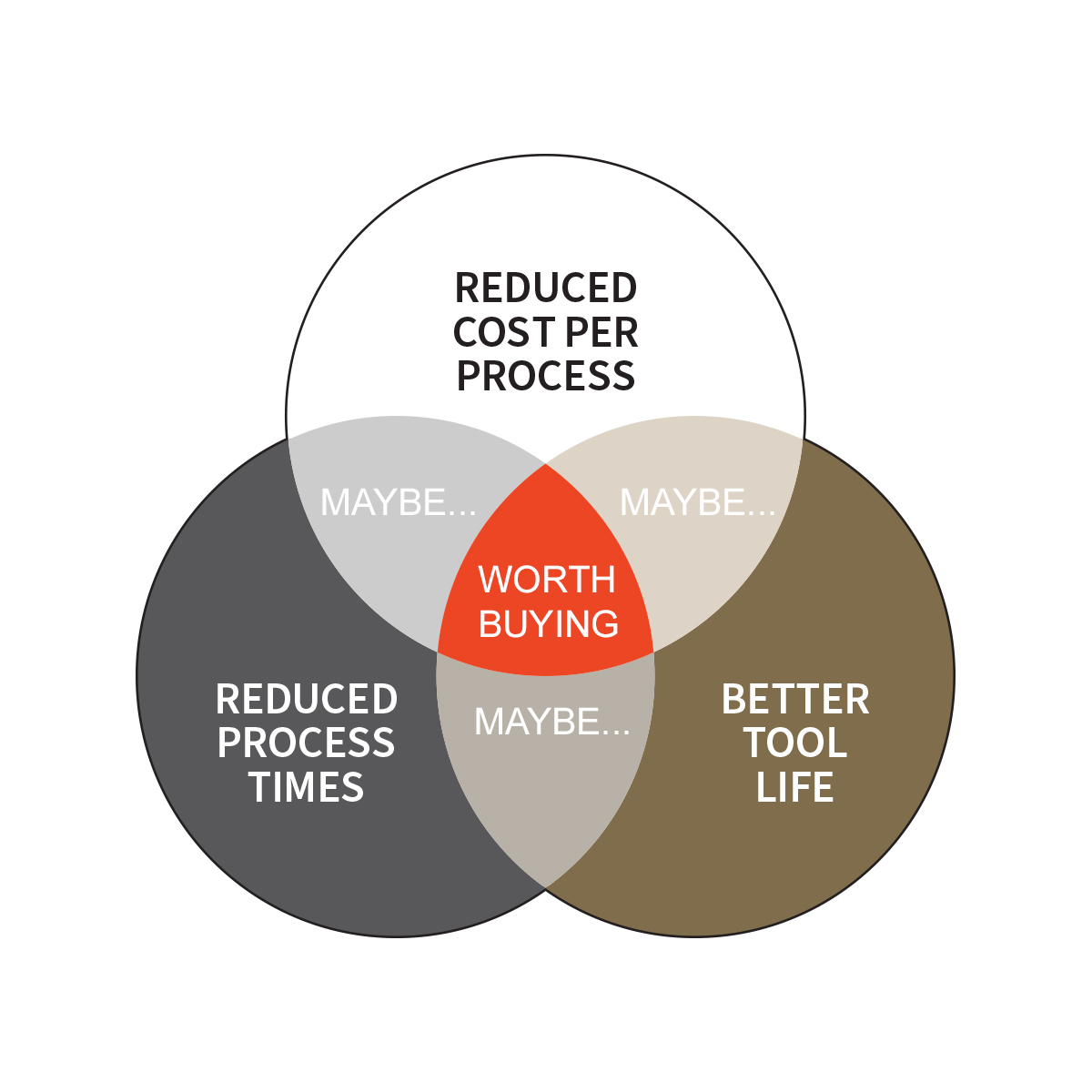
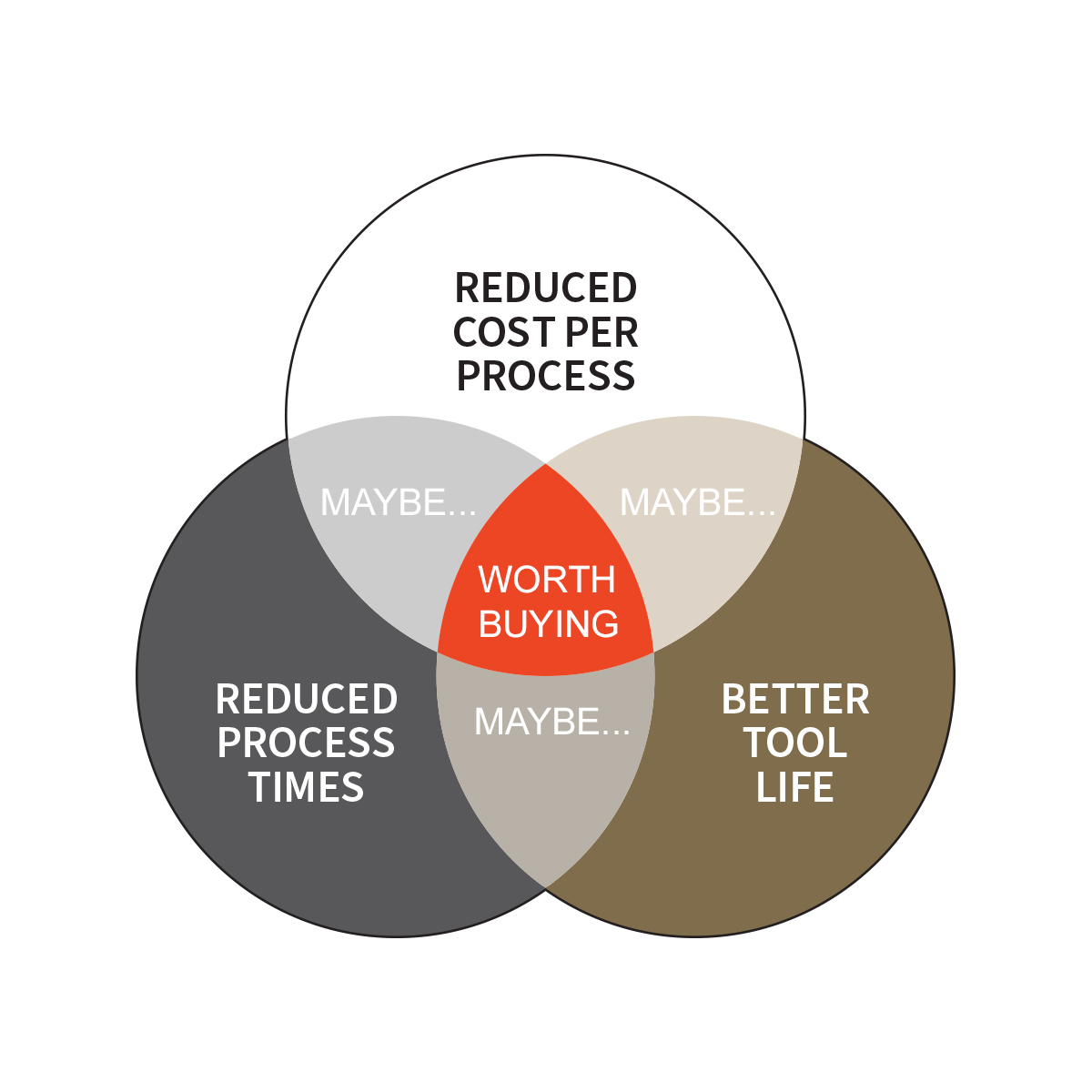
All Drills Are Not Created Equal and AMEC's Acclaimed T-A System Offers Unmatched Advantages
AMEC T-A : CS #1 - TOOL LIFE
Original T-A / Thin Wall Inserts
Structural Steel / Fabricator
AMEC T-A : CS #2 - PRODUCTIVITY & PRODUCTION COSTS
Original T-A / SS Inserts
Structural Steel / Fabricator
AMEC T-A : CS #3 - CYCLE TIME & PRODUCTION COSTS
Original T-A
General Machining
THE CHALLENGE: The customer drills I-beams made from A36 structural steel using a Ficep structural beam drilling machine center with mist coolant. In need of improvements, the customer requested a solution that would provide more tool life from the drill inserts.
OBJECTIVES: Increase Tool Life
WORKPIECE: I Beams, HA300 Structural Steel
HOLE Ø: 22mm
HOLE DEPTH: 11mm
THE CHALLENGE: A customer is a large structural steel and ductwork specialty contractor in the construction industry. They manufacture I-Beams and H-Beams
made from structural steel using a Peddinghaus with soluble oil mist coolant. The customer’s annual production is over 100,000 tons (90,718.5 metric tons)
of steel beams, bars, and ductwork. The customer wanted to increase productivity while decreasing the overall cost of production.
OBJECTIVES: Increase Productivity and Decrease Cost of Production
WORKPIECE: I Beams/H Beams, Structural Steel
HOLE Ø: 30mm
HOLE DEPTH: 20mm
THE CHALLENGE: A customer manufactures printing rolls made from aluminum bar for the label industry. They use a Mori Seiki lathe with coolant through the
tool to produce their products. The customer needed to improve the production
process by reducing the cycle time and decreasing the cost of production.
OBJECTIVES: Decrease Cycle times and Cost of Production
WORKPIECE: Printer Rolls, Aluminium Bar
HOLE Ø: 25.4mm
HOLE DEPTH: 254mm
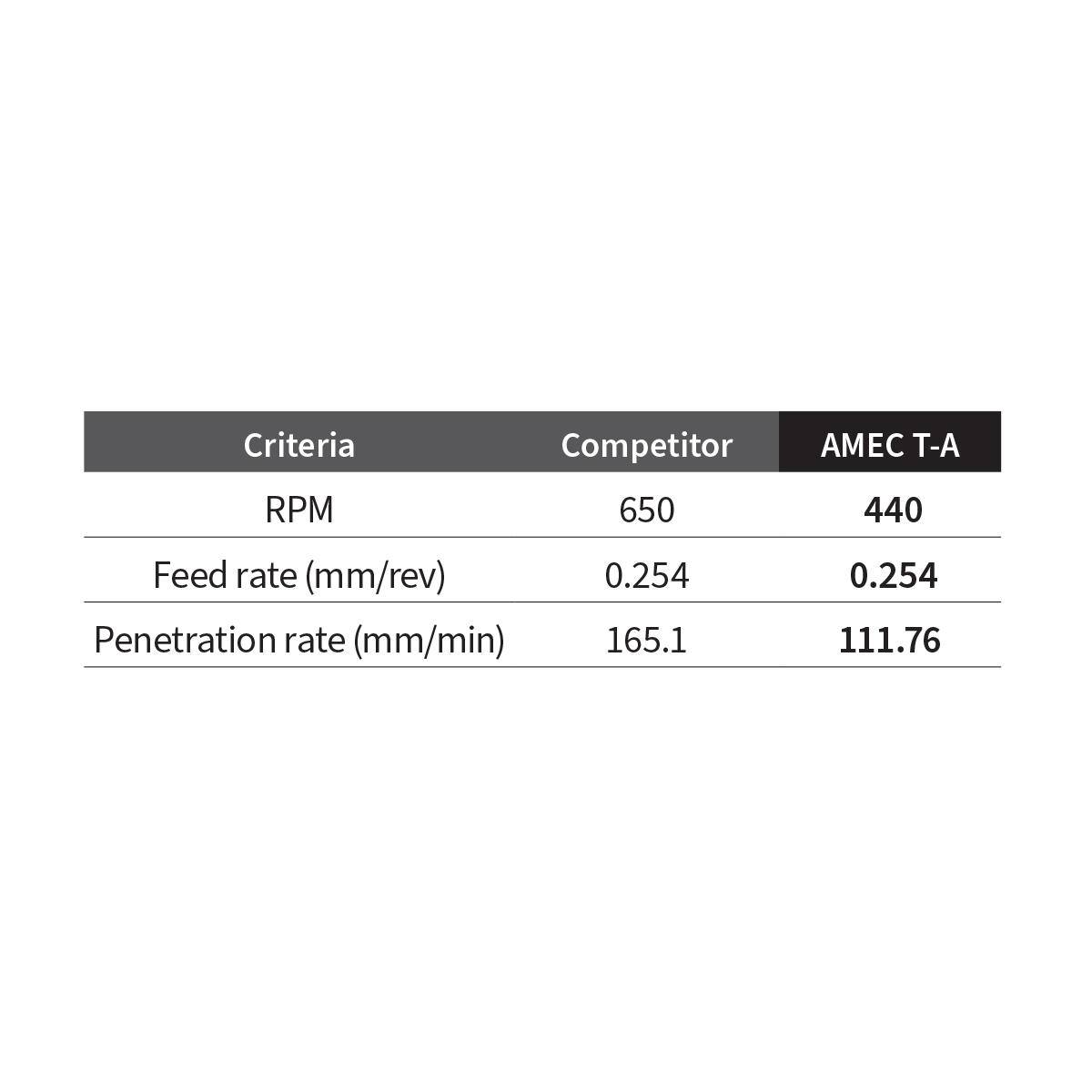
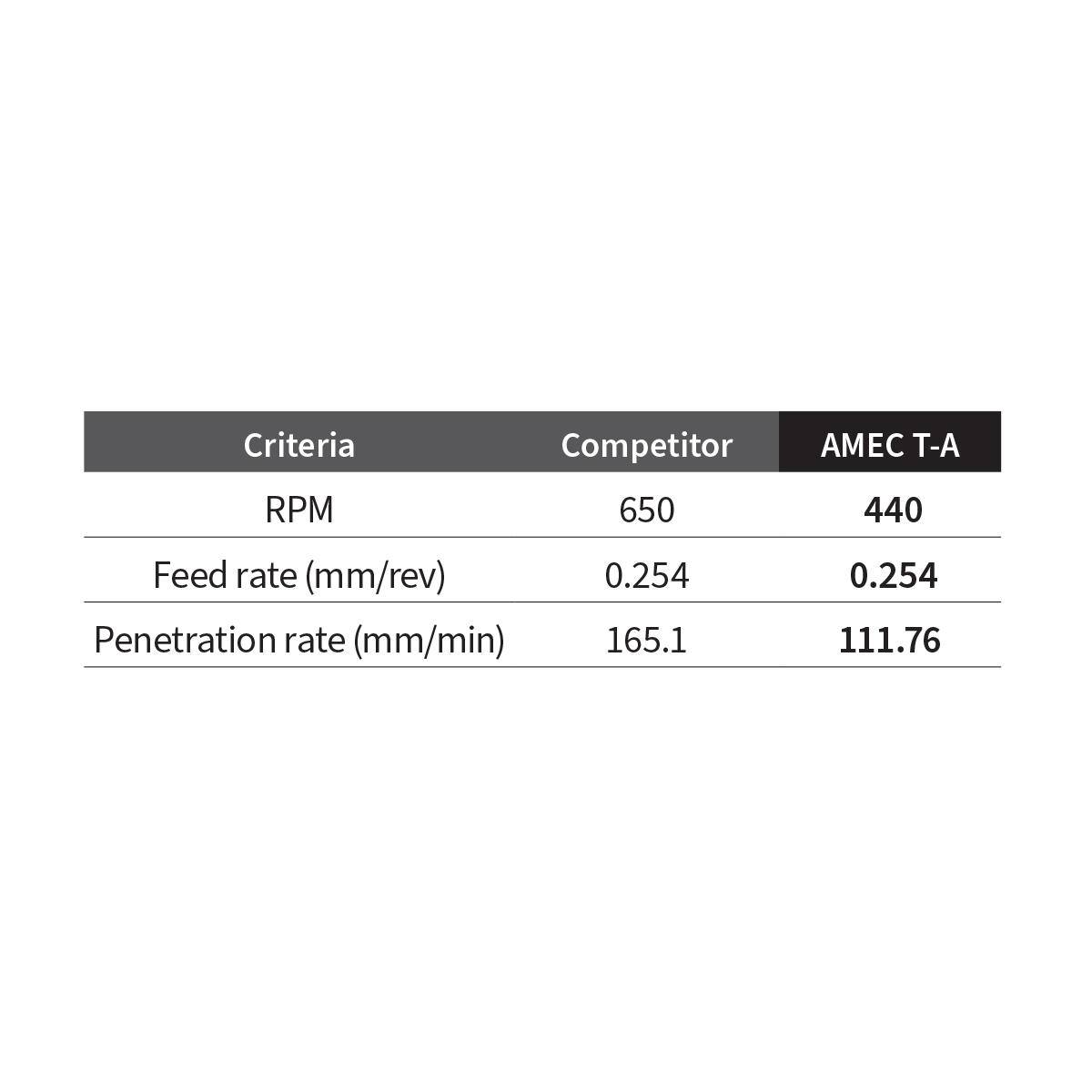
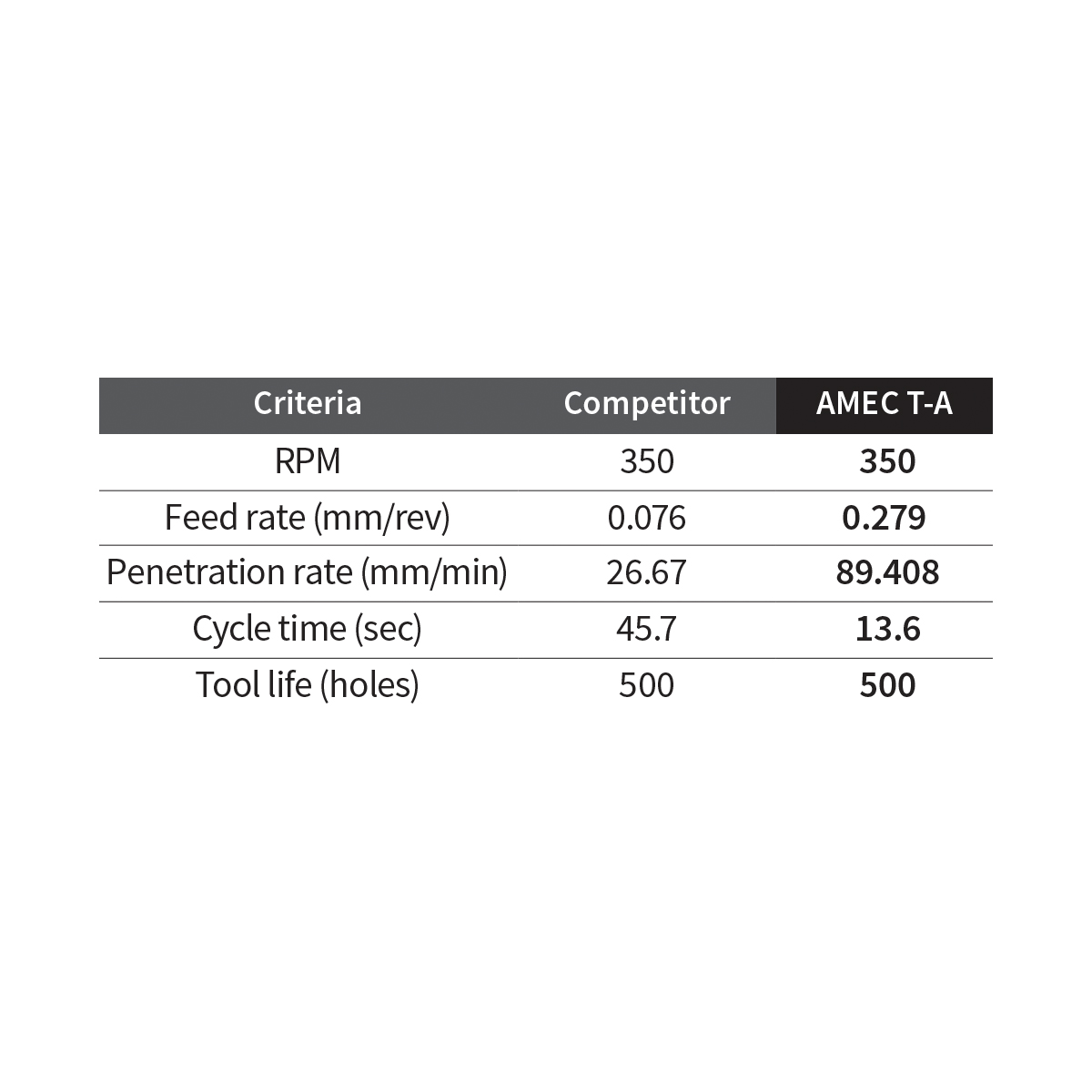
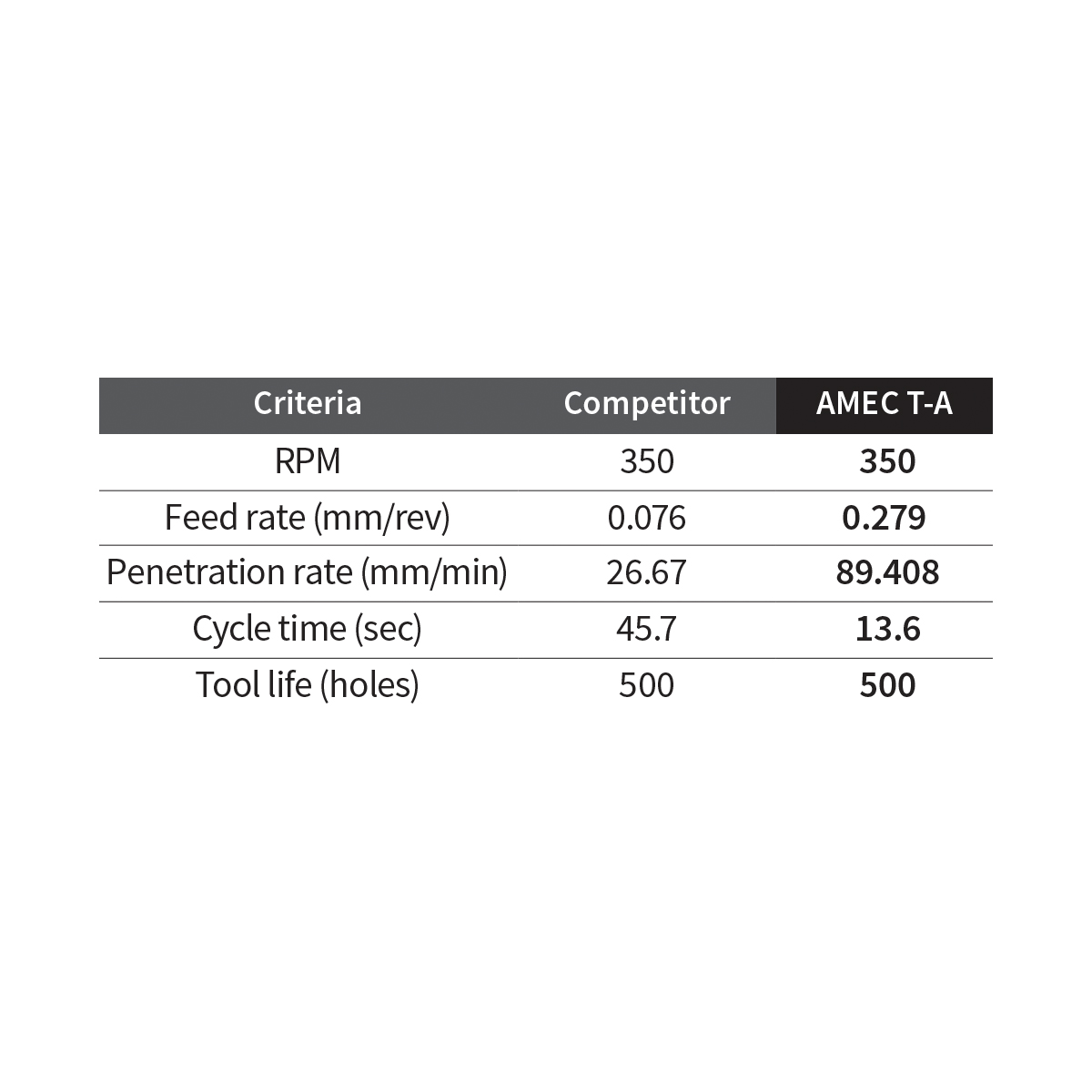
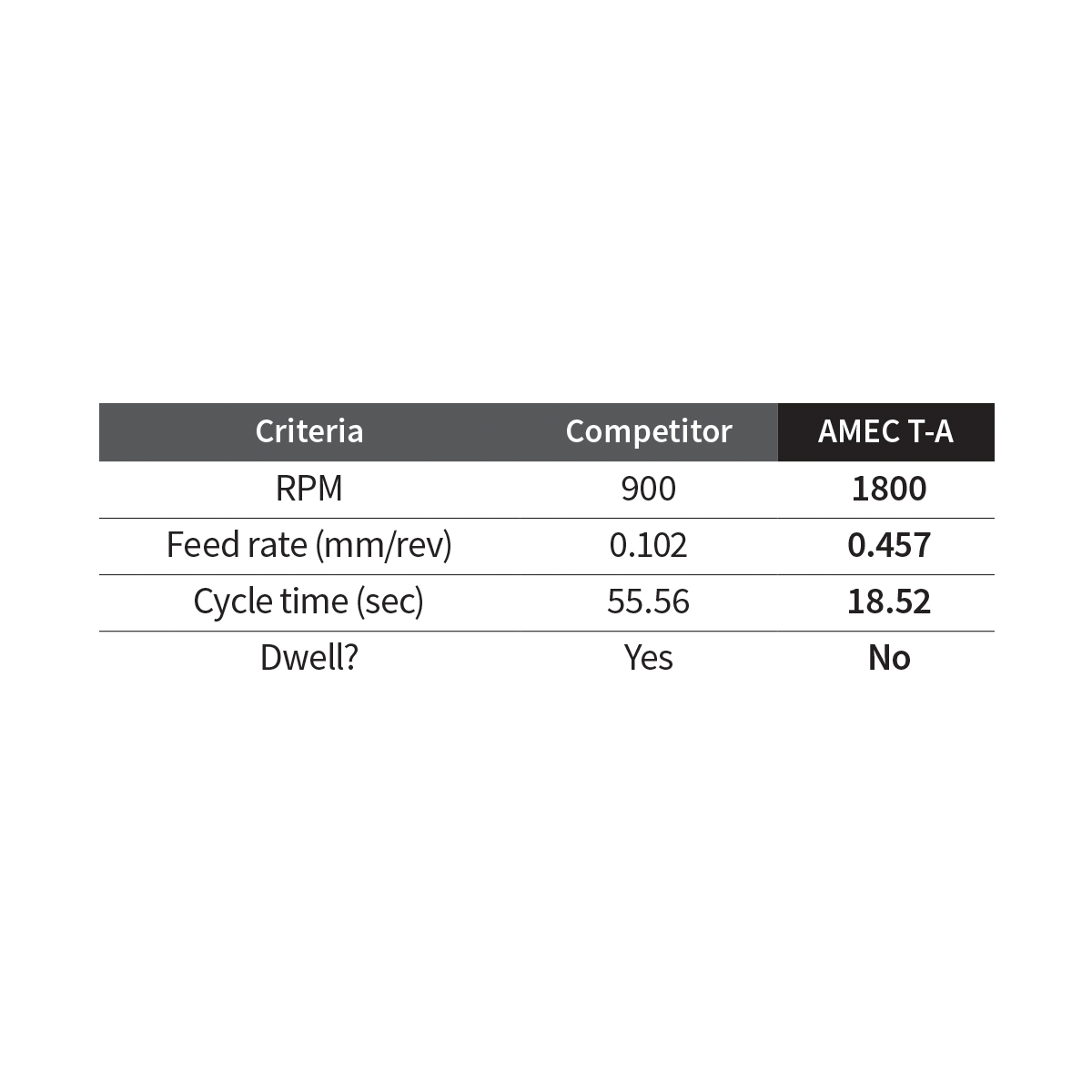
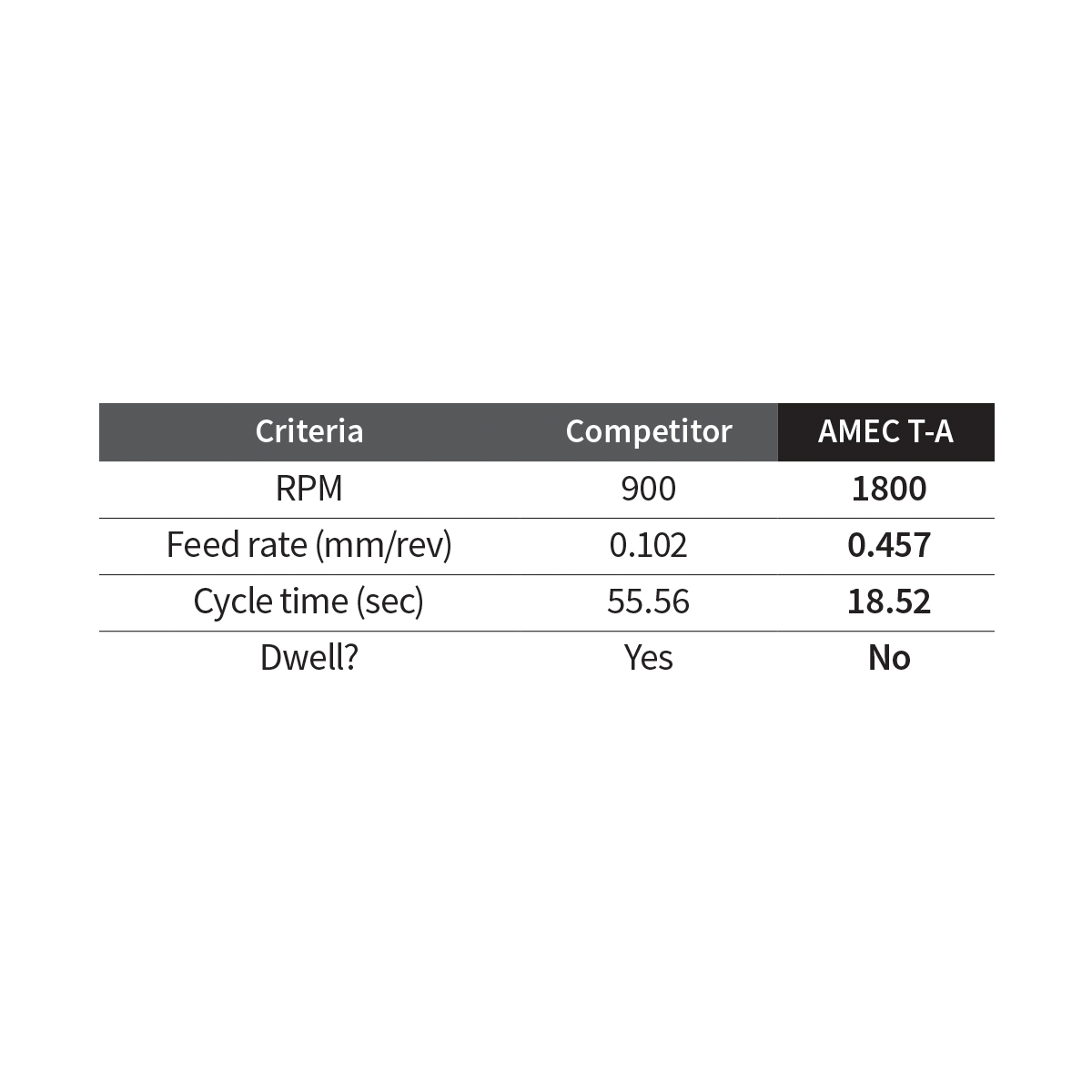
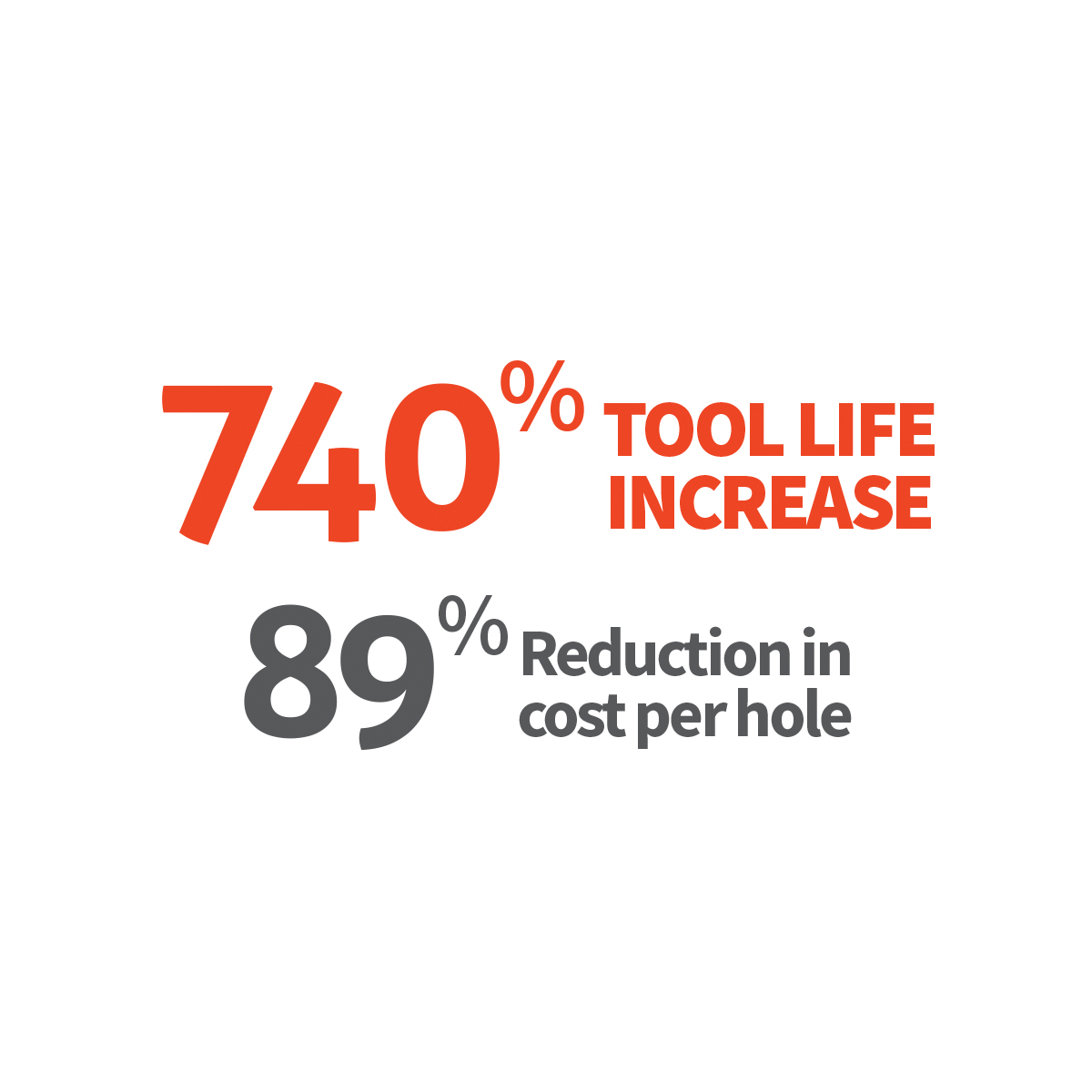
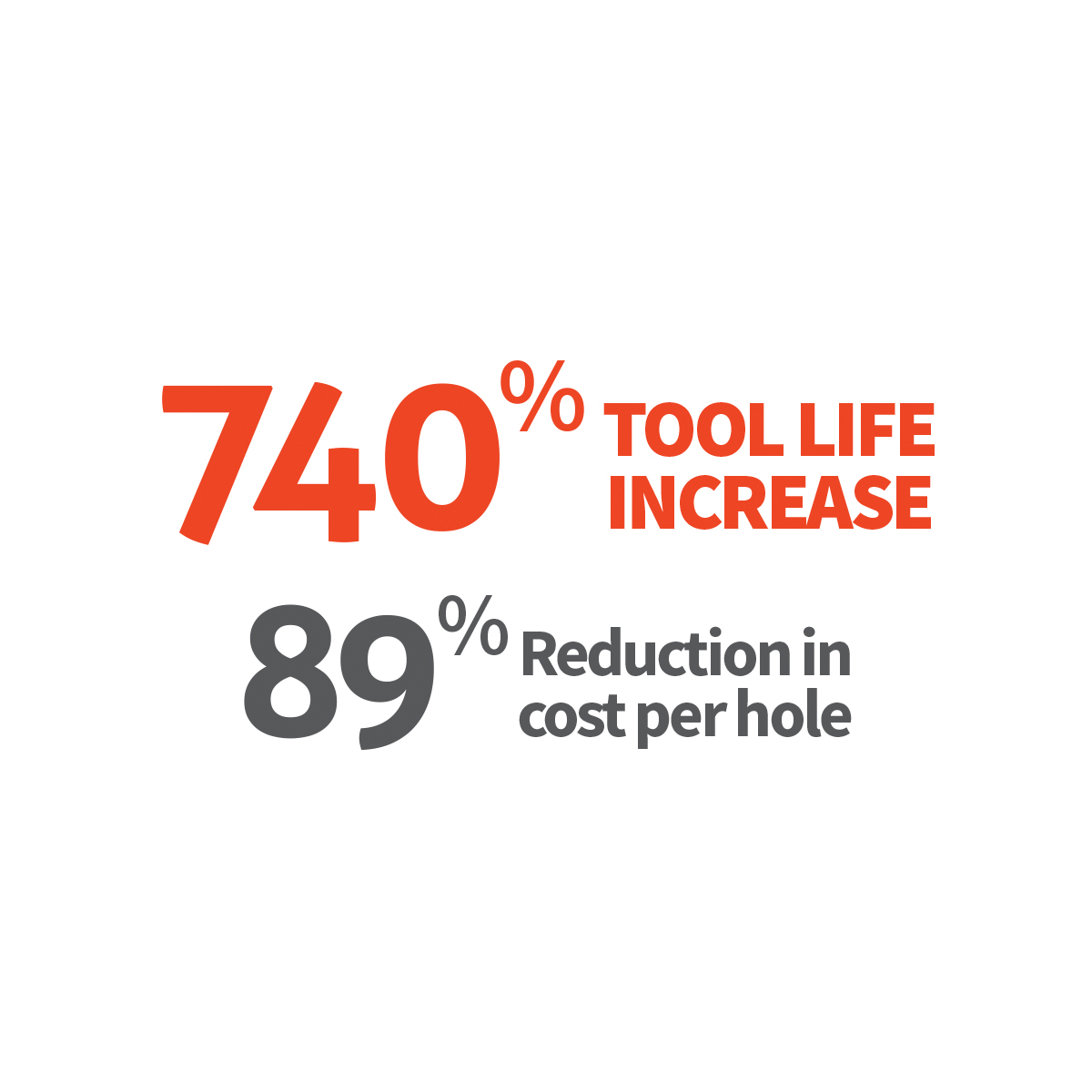
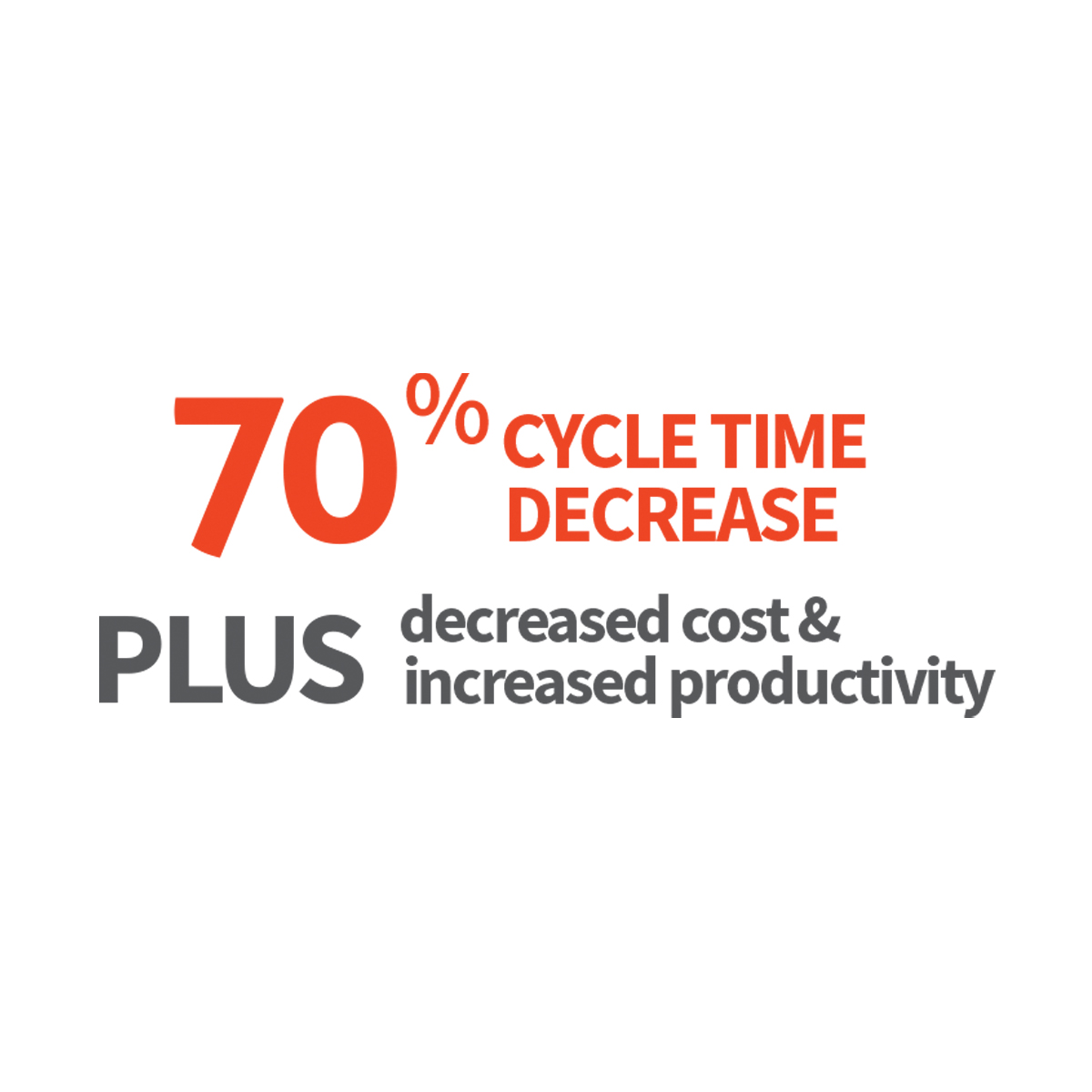
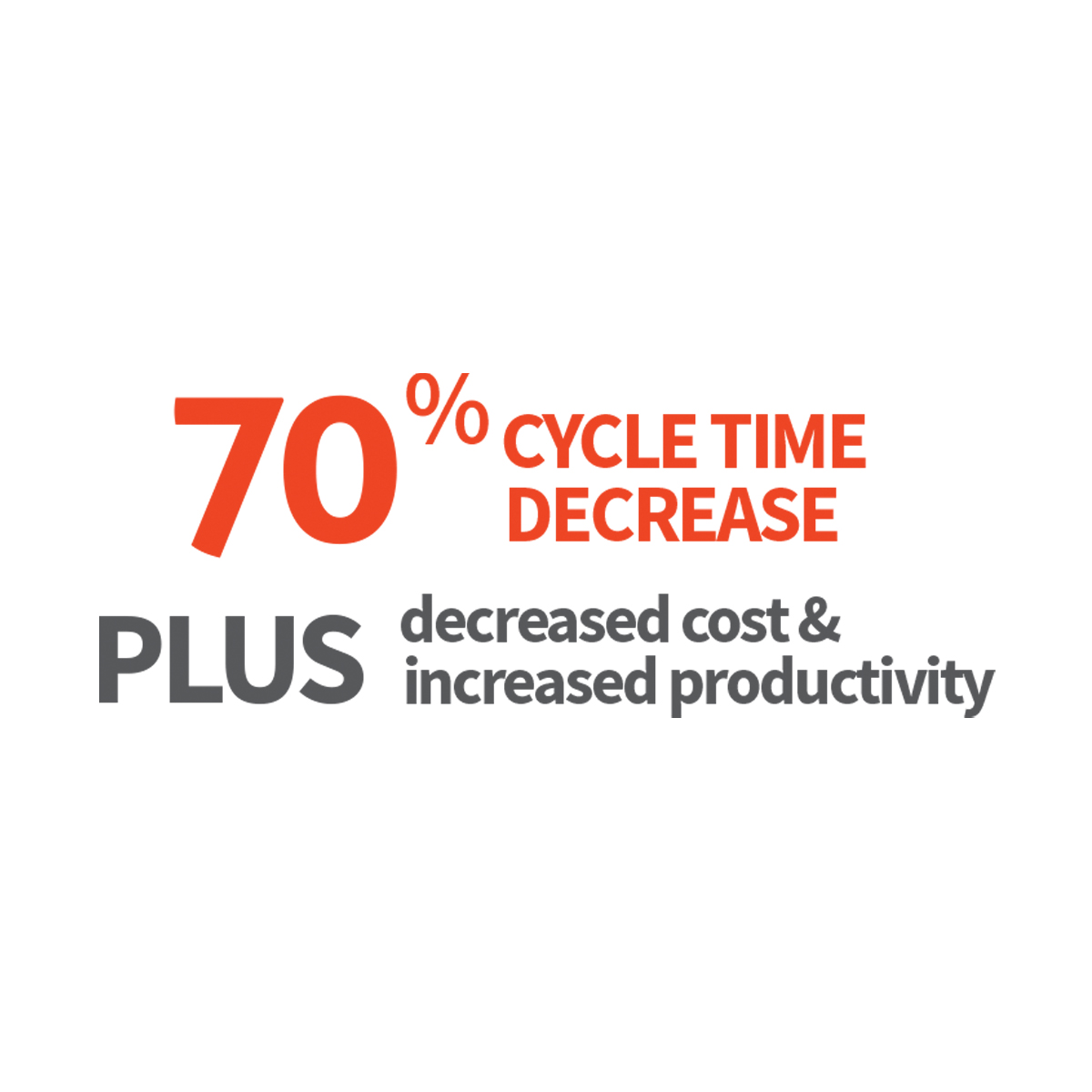
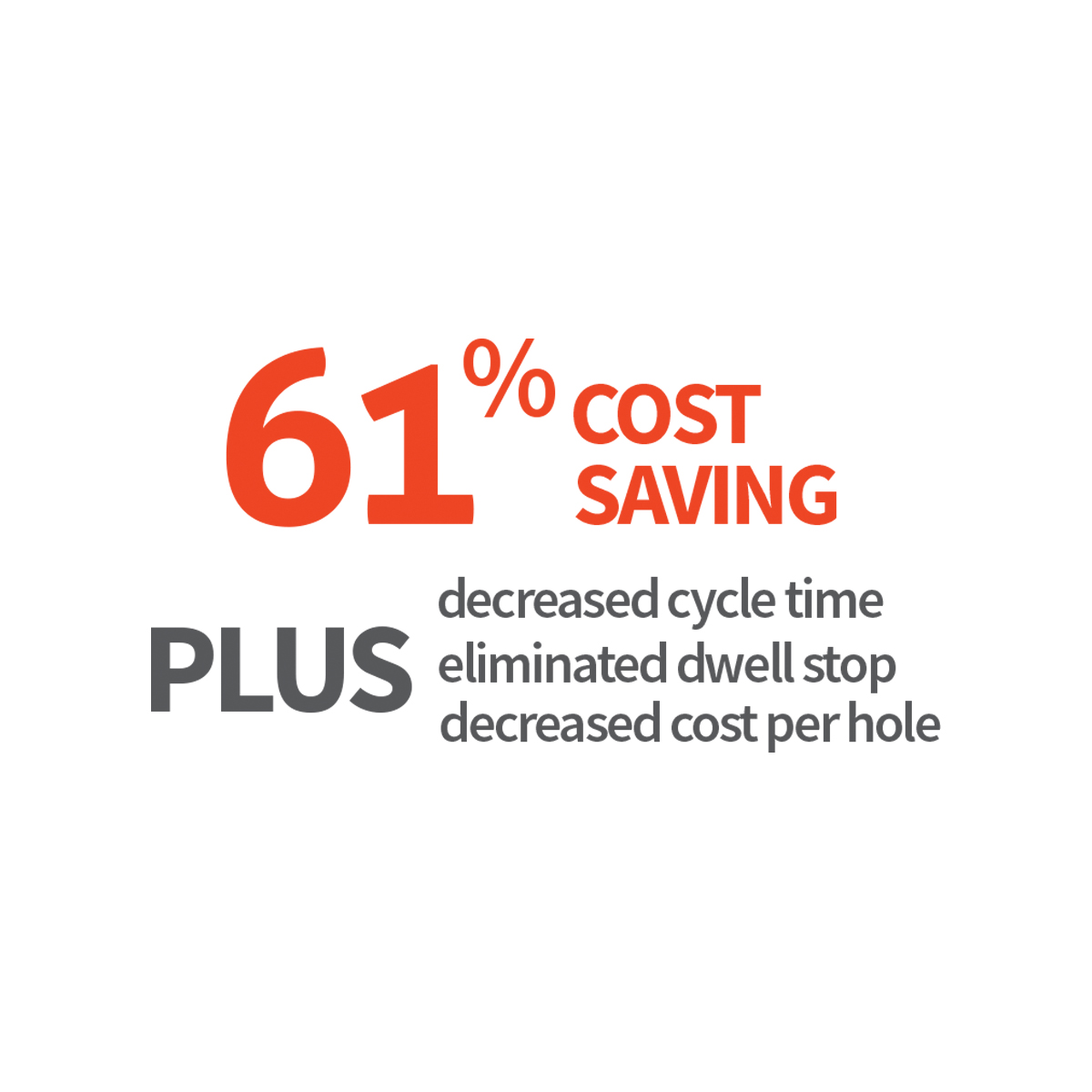
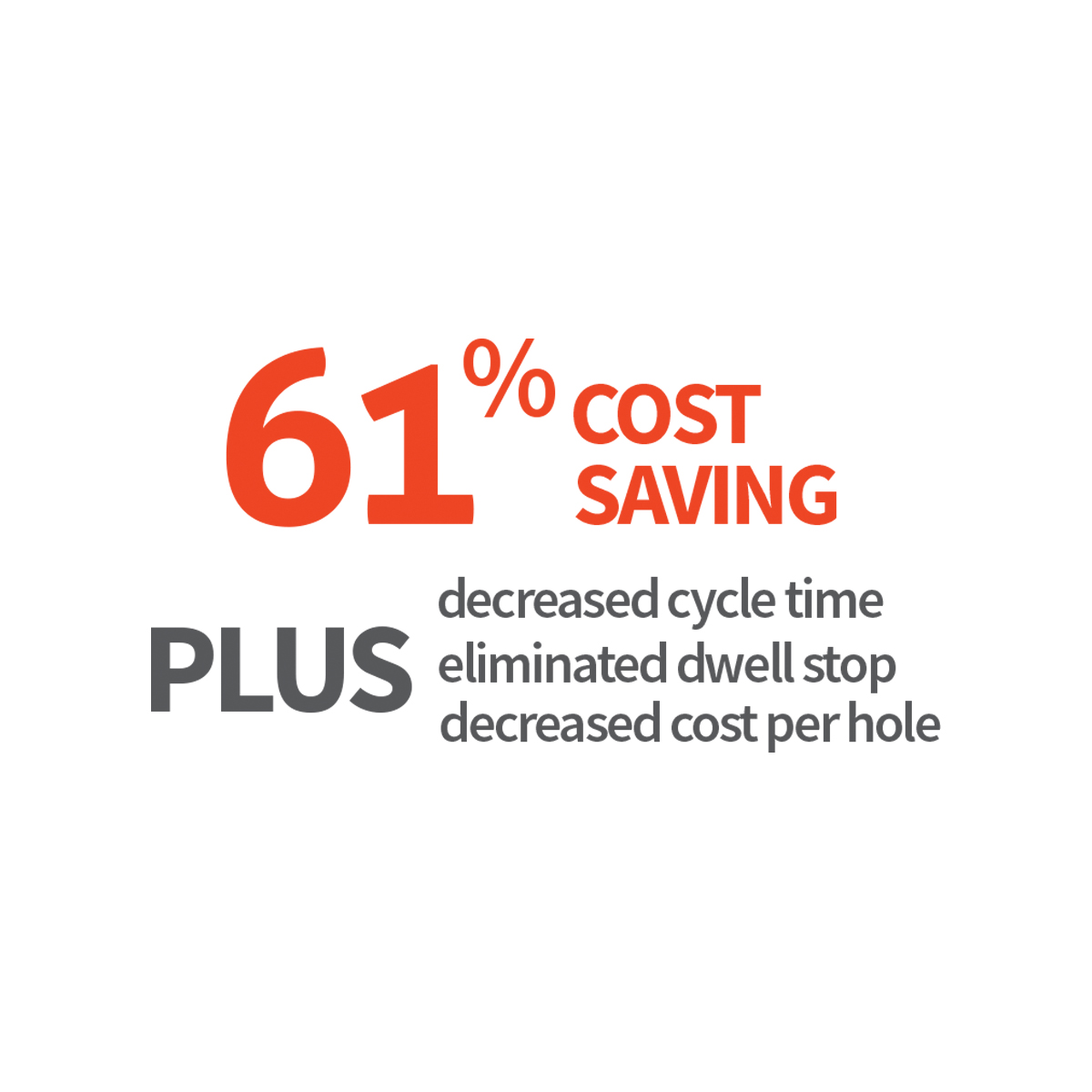