Wouldn’t it be nice if life was simple? Where you could just order “Cutting Fluid Concentrate” and it would fit your requirements perfectly, all you’d need to do would be find the supplier with the lowest price and best delivery service and ‘boom’, job done!
Well, that’s never going to be the case, of course, and anyway, you actually want there to be differences to provide you with a commercial benefit that your competitors may not enjoy. Choice and variety are good, so you need to embrace them and understand how to gain that commercial edge through better suited cutting fluid choices, but that just sounds like a lot of effort!
Don’t worry, we’ve done the hard work for you – here’s a comparison of the different ‘groups’ of cutting fluid and what they’re designed to do. It’s not an advert for any of the types, it’s to help you understand what you need for your machines, so you can make better choices and get more from your spend on these liquid assets. So let’s look at the major differences, with some Pros & Cons for each – but remember these are generalisations and some specific formulations are created for specific atypical requirements, so not every option out there will fit these generalisations.
Mineral or Semi-synthetic or Full Synthetic?
Select from the list below to see more about that oil group.


Mineral oils are derived from crude oil, just like petrol, diesel or plastics, with a proprietary mix of supplementary additives to suit the manufacturer’s purpose. The following lists assume a typical combination of these additives, although they vary considerably – a general pointer to how much ‘additive assistance’ a formulation has is the price. Generally, mineral oil based formulations are at the lower end of the price range but the oil itself is not the main factor in determining the numbers on the ticket, the cocktail of additives needed to make the cutting fluid perform as intended makes up a much bigger portion of the cost.
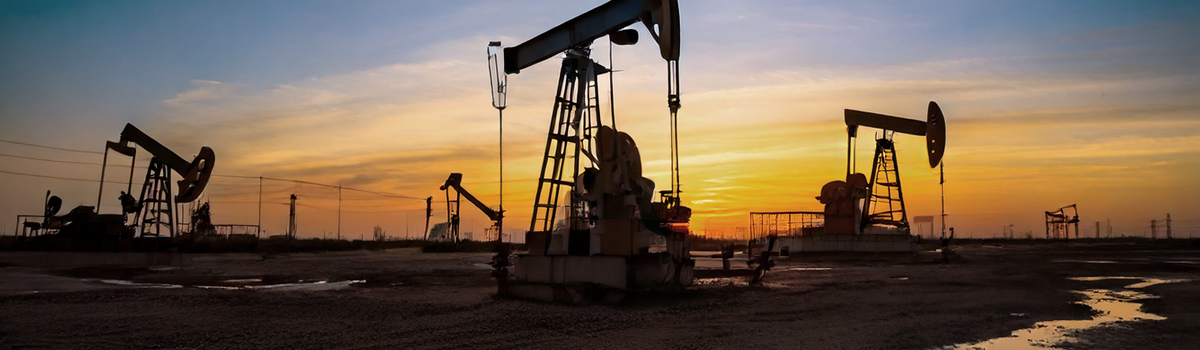
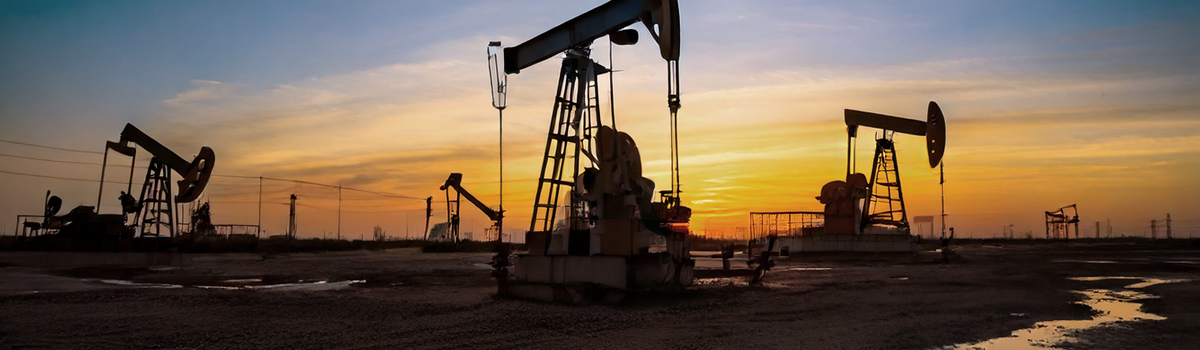
Mineral Oil Pros:
- Good GP choice for general workshops handling a mix of mild steel and non-ferrous material
- Generally lower purchase costs
- Good inherent corrosion resistance
- Often a good option for aluminium and other materials that produce lower machining temperatures
Mineral Oil Cons:
- Mineral oils are a good nutrient source for bacteria, making them more prone to infection
- Mineral-oil polymers are less stable than synthetic so performance durability and sump life are generally lower
- Not a good choice for use with copper or its alloys
- Often not the most environmentally positive choices


Semi-synthetic formulations are, as the name suggests, based on a combination of mineral and synthetic compounds for their lubrication properties. With a reduced requirement for the additives to ‘compensate’ for mineral oil’s potential shortcomings in high-performance operations, the additive package can more easily be designed to provide improved qualities in key areas. Like the Mineral oils, though, the cheaper formulations are much more likely to contain far less in the way of additives, and the following list is a generalisation and as a rule-of-thumb guide, you get what you pay for.
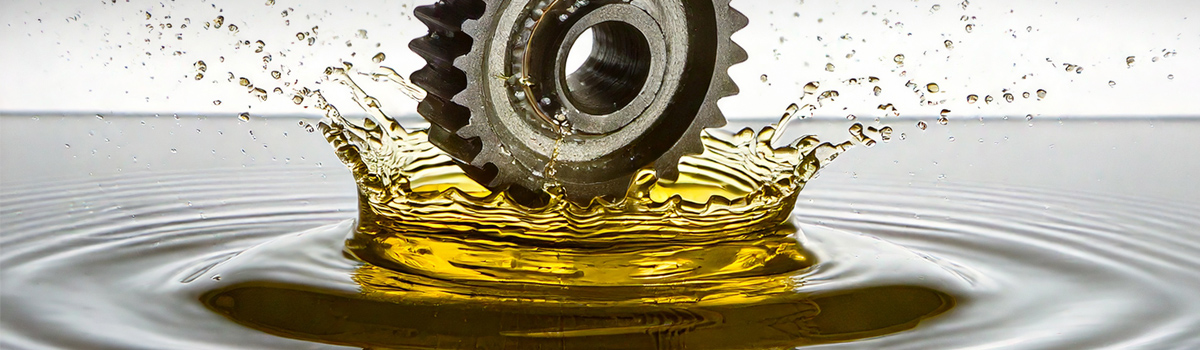
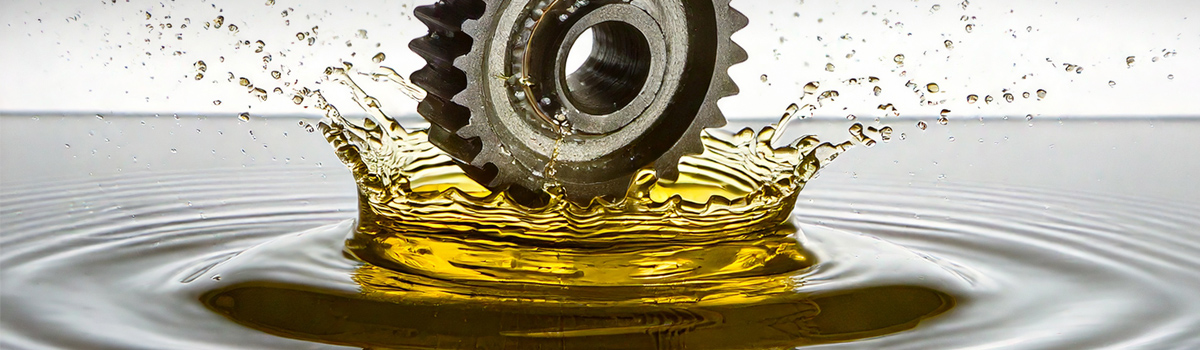
Semi Synthetic Pros:
- Improved lubricity and cooling
- Increased stability and longevity
- Improved chip evacuation
- Improved finish surface quality
- Broader material compatibility
- Typically a less opaque emulsion
Semi Synthetic Cons:
- Higher up-front costs
- Harsher on human health
- Semi-synthetics are not guaranteed to be compatible with each other, so changing may require a full flush


Fully synthetic cutting fluids initially acquired a bad reputation, with first-generation formulations being known as paint strippers that would cause machine problems, but that was a long time ago and modern cutting fluids using synthetic plant-chemistry inspired esters do not have the same issues. Full control over the polymer base allows the additive package to be significantly reduced, making it possible to focus the additive functions in a way that old oil technology never could. Synthetic cutting fluids are genuinely soluble (rather than emulsion-forming) and give a cutting fluid that is clear, with huge benefits for solutions stability and process visibility.
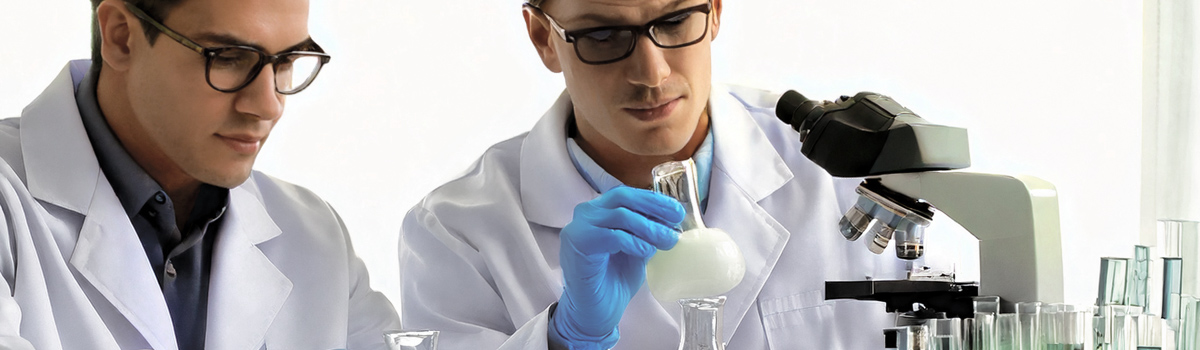
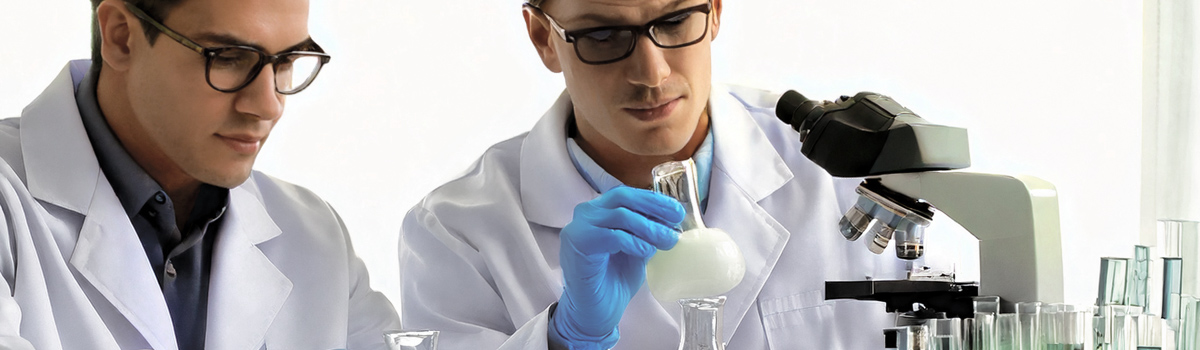
Fully Synthetic Pros:
- Close to double the lubricity of semi-synthetics on ferrous metals
- Greatly increased stability and infection resistance
- Environmentally friendly option
Fully Synthetic Cons:
- Newer technology so higher up-front costs
- Dilution ratios need to be more carefully maintained
- Not necessarily suitable for all water types


Bio-synthetics are a new development in the cutting fluid field and are a modern solution to modern industrial concerns that also bring significant commercial benefits. They are the current benchmark for performance and are particularly suitable to those concerned with the quality of their output, playing a key role in the surface finish while extending performance-durability and sump life to their current limits. Extremely adaptable to specifically-tailored additive packages and being free from the compounds that require additives to mediate their deficits, bio-synthetic formulations are able to provide exceptional extreme-pressure performance and greatly improved lubricity in ferrous and non-ferrous metals.
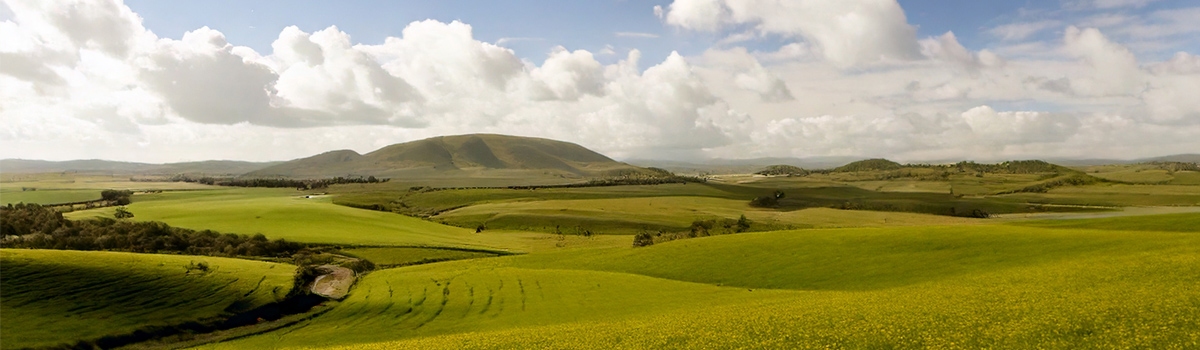
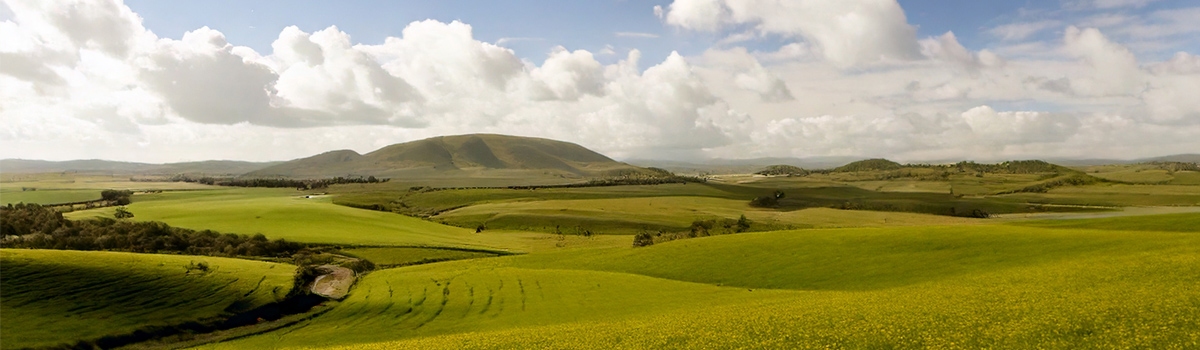
Bio-synthetic Pros:
- Exceptional EP performance and lubricity
- Unmatched tool life potential
- Excellent protection from corrosion with the appropriate additive package
- Biodegradable and environmentally friendly
Bio-synthetic Cons:
- Newest technology so highest investment costs
- Best returns achieved with modern machinery & tooling, so not for everyone


As you can see, there are four easily differentiated major groups of cutting fluid, although within any group the proprietary formulations of the different products will make differences to the suitability of that product to your needs. If you’re looking for the best option for you, what you’re really asking is “which is the most suitable for my situation and work?”. To fully answer this question, you’ll need to take into account your specific situation and add that to the preferences for one of the groups. What does this mean?
That final point we mentioned in the “Cons” of the bio-synthetic provides a clue to what we’re thinking about, where the machinery plays a part in the coolant’s suitability.
Cutting fluids are a fairly complex mix of various chemical compounds, carried around in an emulsion (or solution in some cases) to reach the areas that they are needed. In essence, the ‘oil’ is not really what you’re paying for, certainly in terms of where you want to achieve ROI on the investment. The value lies in those additives that make it possible for the cutting fluid to do its job. Of course, the ‘carrier’ oil will be instrumental in getting those additives to where they’re needed, but the oil alone won’t give the results you’re seeking, however the choice of ‘carrier’ is important as it has be matched to your environment. There’s no point transporting an expensive mix of quality additives around in a base that degrades in water that’s as hard as yours may be, or has the same acidity, or even has the base-level bacterial load that yours may have, meaning that the additives can’t inhibit infection for long enough to get that elusive ROI.
Sure, whatever you buy will work to a degree, but only by getting the one that works best in your circumstance will you get the best ROI from your cutting fluid. And the same sort of thinking need to be applied around your machines and the type of work you tend to do.